Filter House Performance Assessment Saves Full Set of Filters
A Midwestern peaking facility had changed filters less than 18 months earlier only to see progressive turbine output degradation. The Plant Manager of the facility contacted Nederman MikroPul to discuss the issue.
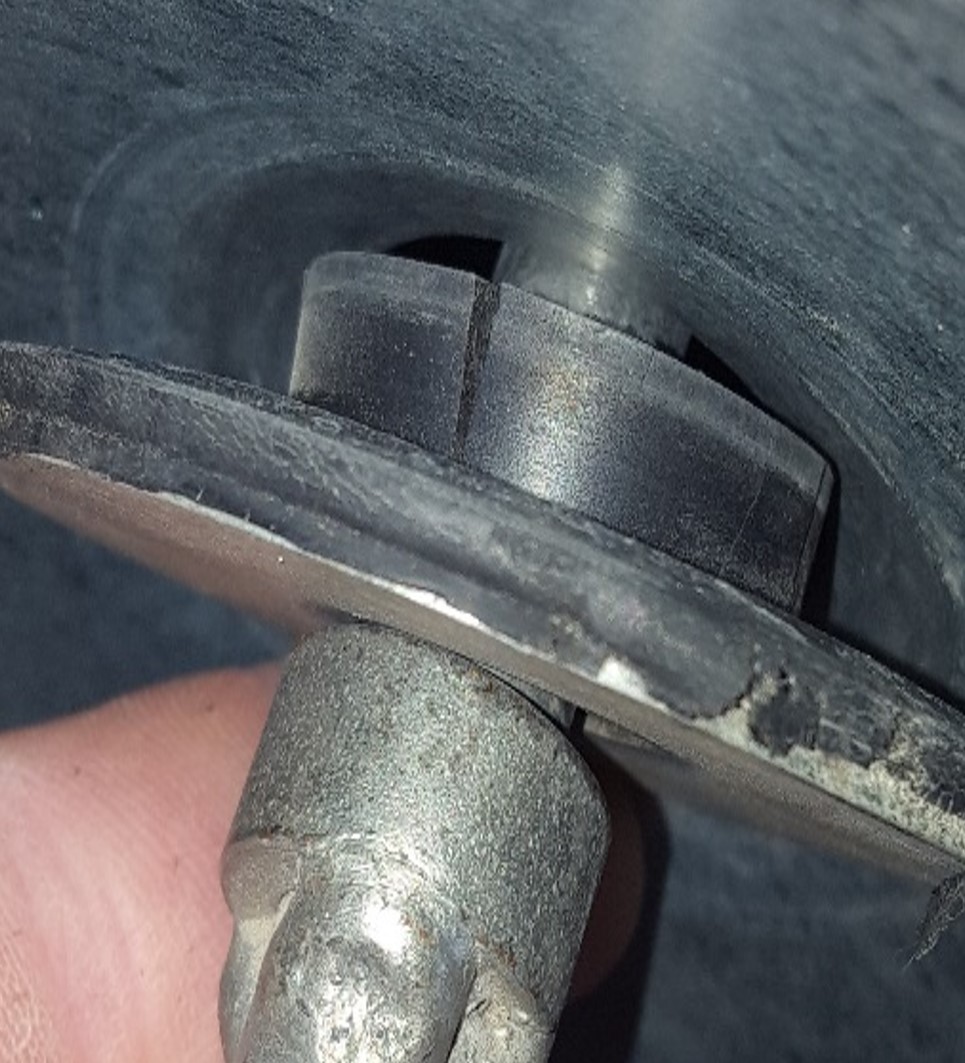
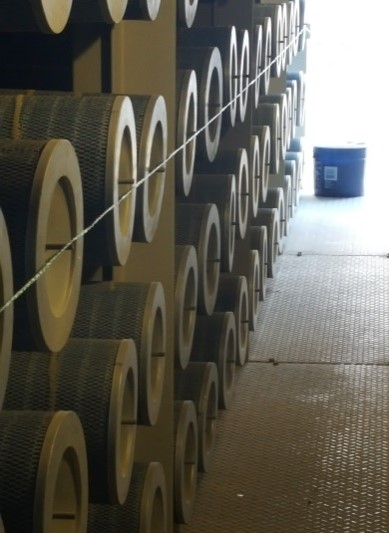
A Midwestern peaking facility had changed filters less than 18 months earlier only to see progressive turbine output degradation. The Plant Manager of the facility contacted Nederman MikroPul to discuss the issue and agreed upon a plan to have a Certified Nederman Field Technician perform a field inspection to help identify any issues that could be contributing to the problem.
Tripod and gasket repairs addressed the bypass condition in all four systems along with recommended repairs to weather hoods and door gaskets.
Every Nederman Mikropul Field Services Technician goes through extensive design and equipment training and is certified for services on all styles of air inlet systems. After issues with improper tripod orientation and damaged gaskets were revealed it was recommended that several sets of filters be sent to an independent lab for testing. Once the gasket had been properly replaced and secured, the filters were confirmed to be in good shape. Nederman was contracted to perform the repairs and properly install filters that allowed all four systems to be up and available before the start of their running season.
Outages are the perfect time to assess maintenance needs and reduce unforeseen and expensive discovery down the road. Photographs along with comprehensive reports allow a full and complete understanding of the maintenance needs and to better prepare budgets and execution of work during future outages.
Below are typical assessment work scopes
Inspection Scope – Self-Cleaning (Pulse) Filter House
Inspection Summary – Dirty Air Side – Self-Cleaning Filter House | ||
Item # | Report Section | Item’s Covered |
1 | Exterior Housing | Housing, weld seams, expansion joint, |
2 | Exterior Weather Hoods | Metal, seams, joints, bird screen, coalescing panels |
3 | Compressed Air Piping | |
4 | Ladder/Stairs/Platform | Signs of corrosion, warpage, cracks |
5 | External Access Doors | Signs of corrosion, debris build up |
6 | Panel/gauges | Condition of lenses, housings, |
7 | Access to Dirty Air Plenum | Exterior of access door, signs of corrosion or warpage |
8 | Interior Access Door | Signs of corrosion, condition of door seals |
9 | Condition of Dirty Air Walkway | Corrosion, cracks debris buildup, signs of moisture |
10 | Supports, angles, beams | Corrosion, cracks, connections, joints |
11 | Horizontal Recognition | Check level and orientation of filters with lazor |
12 | Connecting Hardware | Corrosion, consistency of orientation to bolt |
13 | Gasket Compression | “go” “ no-go” gauge |
14 | Condition of tubesheet | Corrosion, debris buildup, warpage, seams, joints |
15 | Solenoid Boxes | Check for proper seal in panel, corrosion, wiring |
16 | Solenoids | Check wire and hose connection |
17 | Compressed Air Hoses | Check for flexibility, fit |
18 | Interior Weather Hood | Check alignment of bird screens, droplet/mist panels |
19 | Pressure Tap | Inspect penetration of DP piping |
Inspection Summary – Clean Air Side – Self-Cleaning Filter house | ||
Item # | Report Section | Item’s Covered |
1 | Filter Grid | Signs of moisture, Debris settling, gasket Seal |
2 | Filter Grid | Dark Side – Light detection |
3 | Compressed Air Piping | Inspect penetrations for pulse systems |
4 | Structural | Signs of corrosion, warpage, cracks, condition of paint |
5 | Access Doors/portals | Signs of corrosion, leaks |
6 | Control lines/Tubes | Condition of lenses, tube connections |
7 | Drainage Trough | Inspect for debris and standing moisture |
8 | Air Augmentation | Evaporative Cooling Media, Basin, Piping, Valve, Pump, Distribution Header, Droplet eliminators |
9 | Interior Plenum | Inspect walls and floor for corrosion, cracks, connections, joints |
10 | Silencer | Inspection of leading edge of silencer baffles |
11 | nterior – Expansion Joint | Inspect for cracking, leaks, light |
12 | Report | Generate report on findings |
Inspection Summary – Dirty Air Side Static House
Inspection Summary – Dirty Air Side Static House | ||
Item # | Report Section | Item’s Covered |
1 | Exterior Housing | Housing, weld seams, expansion joint |
2 | Exterior Weather Hoods | Metal, seams, joints, bird screen, coalescing panels |
3 | Horizontal Hood Section | Inspect Droplet Eliminators and or Bird Screen |
4 | Ladder/Stairs/Platform | Signs of corrosion, warpage, cracks |
5 | External Access Doors | Signs of corrosion, debris build up |
6 | Monitoring Tube/Pipe | Inspect penetration and orientation |
7 | Access to Dirty Air Plenum | Exterior of access door, signs of corrosion or warpage |
8 | Interior Access Door | Signs of corrosion, condition of door seals |
9 | Condition of Dirty Air Walkway | Corrosion, cracks debris buildup, signs of moisture |
10 | Supports, angles, beams | Corrosion, cracks, connections, joints |
11 | Horizontal Recognition | Check level and orientation of filters |
12 | Connecting Hardware | Corrosion, consistency of orientation to bolt |
13 | Gasket Compression | Check for seal |
14 | Condition of tubesheet | Corrosion, debris buildup, warpage, seams, joints |
15 | External Control Boxes | Confirm operation |
16 | External Gauges | Check if indications on gauge are visible |
17 | Air Hoses and tubes | Check fit |
Inspection Summary – Clean Air Side – Static Filter house | ||
Item # | Report Section | Item’s Covered |
1 | Filter Grid | Signs of moisture, Debris settling, Gasket seal |
2 | Filter Grid | Dark Side – Light detection |
3 | Structural | Signs of corrosion, warpage, cracks, condition of paint |
4 | Access Doors/portals | Signs of corrosion, leaks |
5 | Control lines/Tubes | Condition of lenses, tube connections |
6 | Drainage Trough | Inspect for debris and standing moisture |
7 | Air Augmentation | Evaporative Cooling Media, Basin, Piping, Valve, Pump, Distribution Header, Droplet eliminators |
8 | Interior Plenum | Inspect walls and floor for corrosion, cracks, connections, joints |
9 | Silencer | Inspection of leading edge of silencer baffles |
10 | Interior – Expansion Joint | Inspect for cracking, leaks, light |
11 | Report | Generate report on findings |
Contact us to create your custom solution
Call us at: 704-859-2723 or fill out the form below.