

- Home
- Products
- Gas Turbine Inlet Filters
- Gas Turbine Retrofits
Anti-icing Systems
Anti-icing Systems
Anti-icing modules in turbine inlets prevent ice formation on filter elements, the gas turbine inlet bell-mouth, and other gas path components.
What effect can a cold climate have on a stationary gas turbine generator?
Cooling ambient air can in fact have a positive effect on turbine generator output efficiency due to increased density of the air. For routinely warm climates, gains can be had by cooling the incoming air.
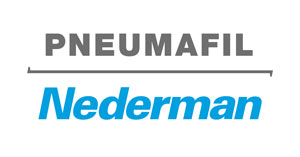
What are the problems if ice forms on a gas turbine generator?
If ice forms around certain areas there are several issues that can occur.
Around the bell-mouth of the turbine, solid ice particles that enter or shed from other inlet components can cause damage to the turbine, resulting in going off-line for expensive repairs. Ability to turndown the output of the turbine may be limited by potential ice formation when inlet guide vanes are in a mostly closed position.
At the entrance to the inlet filter system, icing can plug inlet filters, causing the implosion doors to open (if present on the inlet). This causes the gas turbine to ingest unfiltered air. Icing can also rapidly increase the pressure drop across bird screens, filters, and other inlet components. There may be a performance loss from increased inlet differential pressure, and possible forced outages.
What are the types of anti-icing systems for a gas turbine generator?
COMPRESSOR BLEED ANTI-ICING
A compressor bleed anti-icing system increases inlet air temperature without affecting absolute humidity by using a portion of the compressor discharge air. As a result of compressive forces, this air typically has a temperature of 500°F to 700°F (260C to 371C), depending on the ambient temperature and the gas turbine model.
Compressor bleed anti-icing systems can be retrofitted to an existing generator set
There are two types of compressor bleed anti-icing systems: low pressure and high pressure.
The low pressure system uses one or more low pressure hot air supply duct(s) connected to a series of discharge branch ducts. They are arranged about one meter on center on opposite sides of the supply duct. Both the supply duct and the discharge arms are of constant velocity (tapered cross-section) design. Each discharge arm has a narrow slot running along its top and bottom edges through which the hot air is delivered. The air velocity would be about 5,000 fpm (25 m/s), in the form of an unbroken upward and downward overlapping hot air curtain through which the cold ambient combustion air must pass.
The high pressure system consists of a series of small diameter vertical pipes, welded into a common hot air supply manifold pipe. The vertical pipes are equipped with multiple nozzles or small-diameter orifices that deliver the hot gas. If the pipe array is located upstream of the main inlet silencer, each opening is equipped with a small silencer to lower the bleed air pressure, attenuate the noise and diffuse the gas. In order to accomplish an even flow of hot air out of each nozzle cluster or orifice, it is necessary to maintain a high pressure behind the nozzle clusters or orifices.
What are the relative advantages of low and high pressure anti-icing systems?
Low pressure anti-icing
- Very Low Noise
- Warm and Cool air streams do not stratify
- No effect on pressure drops (On to Off)
High pressure anti-icing
- Good performance across a range of mass flows
- Easily installed upstream of air filter banks, or between filters and inlet silencer, or downstream of silencer
Contact us to create your custom solution
Call us:
Kevin Roller - Sales Manager, Gas Turbine
704-445-7933
Lynda Bartlett - Aftermarket Sales Engineer
706-551-9197
Carolyn Seckinger - Aftermarket Sales Engineer
706-535-5914
or fill out the form below.