

- Home
- Industries
- Metals
Aluminum Smelters
Dust Collection for Aluminum Smelters
The production of non-ferrous metals, such as aluminum, creates unique air pollution control challenges. Our systems solve these unique challenges.
SOLUTIONS
Aluminum occupies an increasing role in the production of food packaging and consumer goods, as well as in Automotive and Aerospace applications. Although aluminum is a highly recyclable material and reduces industrial energy use per unit manufactured, there are still significant pollution control challenges. Producers need to pay attention to effective source capture measures to protect workers and to both particulate filtration and gas removal devices.
Primary Aluminum
As with most mining and mineral applications, Mikro-Pulsaire baghouse dust collectors are trusted solutions along with Venturi Scrubbers
Secondary Aluminum
Stages of Aluminum Processing
Pretreatment
MikroPul baghouses are accepted as leading solutions for:
- Occupational Health & Safety of workers in the recycled scrap processes including sorting, crushing, milling, and screening operations
- Air Pollution Control in “drying” (delacquering) and “sweating” operations that produce Aluminum separated from coatings and higher melt point materials
- Pollution Control in dross handling from primary processes
- APC in Sweating furnaces
What particulate matter can be present?
Metallic, non-metallic particles. Oxifdized Aluminum fines from dryers. Gaseous pollutants including volatile organic compounds (VOCs). Fumes from incomplete combustion.
Both Mikro-Pulsaire and FS Series baghouse dust collectors are equally at home in pretreatment operations.
Before and After Dust Collection
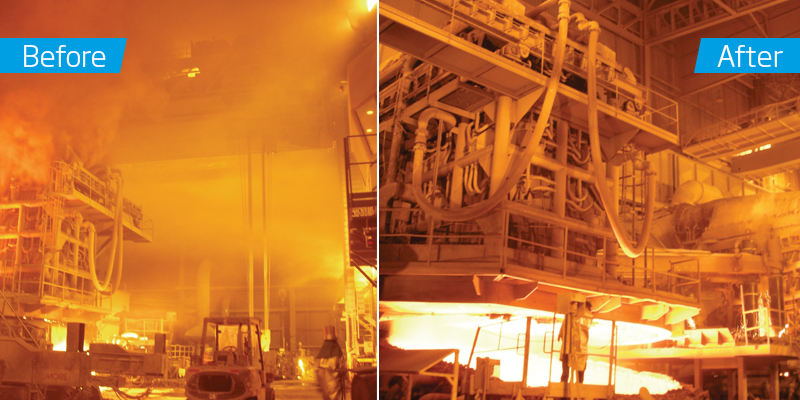
Smelting and Refining
Aluminum processes face unique air pollution control challenges. Gas streams range from ambient to over 500° F (260° C) and may contain high levels of oil, soot, moisture and acids. Airborne Particulate is often submicron in size, abrasive and hygroscopic in nature. The Non-Ferrous industry is highly regulated for particulate emissions as well as various gaseous emissions such as HCl, HF and SOx.
What particulate matter can be present?
Airborne Particulate is often submicron in size, abrasive and hygroscopic in nature. Gaseous pollutants include CO, CO2, Sulphuric Oxide and Nitrogen oxides.
MikroPul FS series baghouse dust collectors are a proven solution for smelting and should be augmented with integral additive dosing systems to remove HCl, HF and SOx.
It is possible that Hazardous Air Pollutants (HAPs) may be present yet quantities are hard to enumerate. These can include Lead, Nickel, Chromium, Cobalt, Selenium, Cadmium and Arsenic.
Use FS dust collectors also for demagging and degassing operations, fluxing, allotting and pouring.
All MikroPulsaire and FS dust collectors are supplied with MikroPul-Assist remote monitoring providing 24/7/365 access to notifications about filter performance.
Case Studies

Fume Treatment for Aluminum Melting
8/14/2019
Case Study: FS baghouse dust collection system for Xiashun China
Dangers of Aluminum Dust
Aluminum dust also can be combustible or explosive if it becomes suspended in the air at the right concentration.
Even if pure, non-ferrous aluminum is used, sparks can occur during an aluminothermic reaction, also called a thermic reaction. Such a reaction occurs when an aluminum particle and a metal oxide, such as rust, are ignited by a heat source and chemically burn as a "Class D" fire (i.e., combustible metal). The reaction is similar to a fireworks explosion, can create 4,500ºF sparks, and can occur when a grinder is used on ferric material (e.g., steel) prior to being used on an aluminum material or vice versa. This type of sparking and associated fire hazard may be eliminated by restricting the use of a grinder to only one type of material. In the absence of that safeguard, if grinding under these circumstances creates sparks, then it is considered hot work and a fire watch would be required under any of the circumstances described in 1915.504(b).
Grinding aluminum also can create housekeeping issues. An aluminothermic reaction can occur in situations where there is an accumulation of powder or dust from the grinding operation. A shipyard environment typically contains metal oxide, in the form of rust, and a heat source, in the form of welding, cutting, brazing, or grinding. If enough aluminum powder is introduced, there is a potential for a significant aluminothermic reaction. In an Australian Department of Energy "lessons learned" article, "Fireball from Aluminum Grinding Dust," an individual received first- and second-degree bums on his hands and head from a fireball that developed while grinding a piece of angle iron a few days after another individual ground the heads off approximately twelve aluminum pop rivets. This type of accident may be prevented by employing good housekeeping habits in addition to using material-specific tools.
For grinding and housekeeping of fine aluminum dust visit our sister site nederman.com
Contact us to create your custom solution
Call us at: 704-859-2723 or fill out the form below.