Case Study: Enhancing Dust Collection for a Home Exterior Products Manufacturer
A company specializing in manufacturing home exterior products was facing a significant challenge in maintaining safe and efficient operations due to an aging system.
Product: Baghouse Dust Collector, Ductwork, Explosion Safety Equipment
Key Benefits: Energy Savings, Smaller Footprint, Increased Efficiency and Safety
Customer Challenge
The existing dust collection system consisted of two outdated dust collectors, which were struggling with low pressure drops and inadequate for managing the combustible wood dust. These limitations were not only impacting production capacity and air quality but also posing a significant risk for workplace safety.
The customer aimed to increase production output, enhance airflow, and replace the two inefficient dust collectors with a single, more powerful unit. The primary objective was to achieve these improvements while ensuring compliance with stringent safety standards for combustible dust. Additionally, the company sought a solution that would allow them to recycle clean air back into the building during the winter months to reduce energy costs associated with heating.
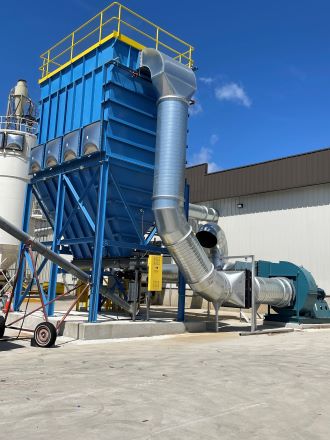
Nederman MikroPul's Solution
Nederman MikroPul, a leader in industrial air filtration solutions, addressed these challenges. Recognizing the complexities involved, Nederman MikroPul provided comprehensive engineering services to design a complete dust collection system. This solution extended from the dust pickup points throughout the facility, all the way to the exhaust.
The new system featured a high-capacity dust collector with an airflow of 30,000 cubic feet per minute (CFM), effectively consolidating the function of the two outdated collectors into one larger, more efficient unit. The dust collector was equipped with an Isolation Flap Valve on the dirty side, designed to prevent any potential explosions from propagating back into the building. The clean exhaust side was fitted with a Quenching Valve (QV), providing another layer of safety by rapidly quenching any flames in the event of a deflagration.
To further enhance safety, multiple explosion panels were integrated into the dust collector, along with advanced safety instrumentation to monitor and respond to any signs of combustion. This comprehensive approach ensured that the new system met or exceeded all relevant safety regulations for combustible dust.
Project Scope
- Engineering Study: A detailed engineering study was conducted to assess the facility's specific dust collection needs, airflow requirements, and safety considerations.
- Dust Collector Design: A new dust collector was custom designed to handle the higher airflow requirements and to operate efficiently within the constraints of the available space. The design incorporated explosion safety features, ensuring both compliance with regulations and protection of the facility and its workers.
- Ductwork: Comprehensive ductwork was designed and installed to ensure optimal airflow from the various pickup points throughout the manufacturing process to the dust collector, minimizing pressure losses.
- Explosion Safety Devices: Given the combustible nature of wood dust, the new system was equipped with explosion safety devices, including the Isolation Flap Valve, Quenching Valve, multiple explosion panels, and advanced safety instrumentation. These devices were strategically integrated to provide a robust safety barrier against any potential dust explosions.
Results
The implementation of Nederman MikroPul's solution resulted in several significant benefits for the customer. The new dust collector provided a substantial increase in airflow, effectively handling the wood dust produced during manufacturing processes. This improvement enabled the company to boost production capacity without compromising on safety or air quality and reduce footprint using only one dust collector.
Moreover, the ability to return clean air back into the building through a HEPA filter provided substantial energy savings, particularly during the winter months. By recycling warm air, the company reduced its reliance on external heating, leading to lower energy consumption and costs.
Overall, the project successfully achieved the customer's goals of increasing production, enhancing safety, and reducing energy usage. Nederman MikroPul's comprehensive approach, combining engineering expertise with innovative dust collection technology, provided a robust and sustainable solution tailored to the specific needs of the home exterior products manufacturer.
They have been running the new system for several months and are very happy with the outcome of the project.
Contact us to create your custom solution
Call us at: 704-399-7441 or fill out the form below.